Shell Becomes First European Company to Receive Third-Party CE Certification for In-House 3D Printed Part
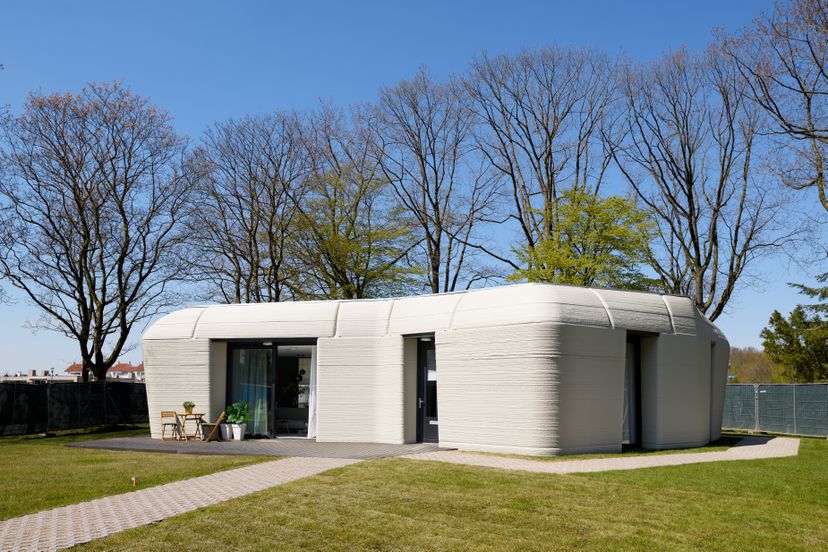
Oil and gas giant Royal Dutch Shell has reportedly become the first company in Europe to obtain CE certification from a third-party authority for a part 3D printed in-house. The part in question is a 3D printed pressure vessel that has been certified in accordance with the European Pressure Equipment Directive (PED).
CE certification is a mandatory conformity mark for products sold within the European Economic Area (EEA). It confirms that products meet all applicable safety, health, and environmental requirements, allowing them to be sold and distributed within the EEA.
With the certification, Shell has demonstrated that its 3D printing technology can produce parts to the same safety standards as conventional manufacturing methods. This represents a significant milestone for the adoption of 3D printing in safety-critical industries such as oil and gas.
The part that received the CE certification is a pressure vessel used in the oil and gas industry. Pressure vessels are widely used in oil and gas processing, storage, and transportation operations. They are subjected to high pressures and temperatures and must meet strict safety standards to ensure they do not rupture or leak.
By using 3D printing to manufacture the pressure vessel, Shell was able to reduce the lead time and cost of production while ensuring the part met the required safety standards. This demonstrates the potential benefits of 3D printing in industrial applications, where traditional manufacturing methods can be slow and costly.
The certification was obtained from Bureau Veritas, a third-party certification authority. Bureau Veritas performed rigorous quality control and testing of the 3D printed pressure vessel to ensure it met the PED requirements. This involved destructive testing, non-destructive testing, and visual inspection.
The certification demonstrates that 3D printing technology can meet the high safety standards required in the oil and gas industry. This could result in more widespread adoption of 3D printing in the industry, unlocking new opportunities for innovation and cost savings.
Shell's certification is not the first for 3D printing in the oil and gas industry. In 2018, Siemens Energy received certification for a 3D printed steam turbine component, which was also produced in accordance with PED requirements. However, Shell's certification is notable for being the first in Europe and for the use of in-house 3D printing technology.
Shell has been a pioneer in adopting 3D printing technology in the oil and gas industry. The company has been using the technology to produce spare parts for its offshore platforms since 2012. By 2018, it had printed more than 1,000 spare parts using 3D printing. This has enabled the company to reduce lead times for spares and reduce its inventory of spare parts, resulting in significant cost savings.
The use of 3D printing in the oil and gas industry has grown rapidly in recent years. The technology is being used to produce not only spare parts but also complex components such as impellers and heat exchangers. The benefits of 3D printing include reduced lead times, reduced costs, and the ability to produce complex shapes that cannot be made using traditional manufacturing methods.
The certification of Shell's 3D printed pressure vessel represents a significant step forward for the adoption of 3D printing in industrial applications. It demonstrates that the technology can meet the high safety standards required in safety-critical industries such as oil and gas. This could lead to more widespread adoption of 3D printing in the industry, unlocking new opportunities for innovation and cost savings.
In conclusion, Shell's certification for its in-house 3D printed pressure vessel is a significant achievement for the 3D printing industry. It demonstrates that the technology can meet the high safety standards required in safety-critical industries such as oil and gas. This could lead to more widespread adoption of 3D printing in the industry, unlocking new opportunities for innovation and cost savings.